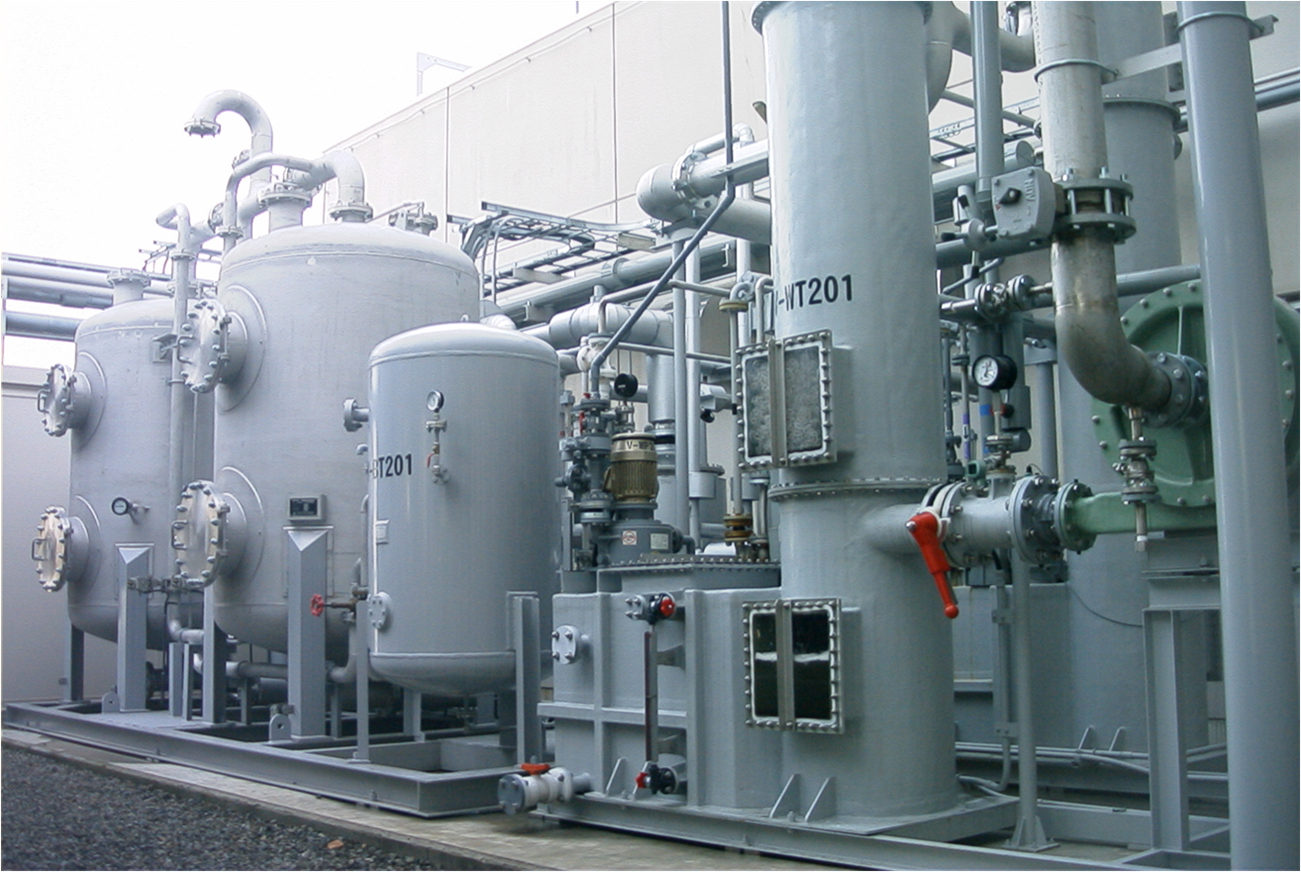
VOC Recovery Facilities
Based on multiple technologies we have cultivated through construction of VOC recovery facilities, we are able to propose a system meeting the air volume and concentration.
MGC Pure Chemicals Taiwan, Inc. (MPCT), a manufacturer specializing in high-tech fine chemicals for the semiconductor and electronic industries, has decided to construct a new hydrogen peroxide production plant in response to the expansion of the semiconductor market. We have delivered Solvent Recovery Units for the hydrogen peroxide production plants at Mitsubishi Gas Chemical Company, Inc. in Japan, and based on the recognition of our expertise, MPCT has awarded our company the contract for Solvent Recovery Unit in Taiwan.
This Solvent Recovery Unit is designed to recover over 95% of valuable solvents from the raw material gas of the hydrogen peroxide production. It utilizes the Temperature Swing Adsorption (TSA) system licensed from CMI Europe Environment (AMCEC) to separate and recover solvents from the raw material gas.
Our scope of work involved basic design, major equipment procurement, and commissioning supervision, and site construction is carried out by local constructor under the customer. Shortly after receiving the award, a global pandemic occurred, necessitating remote management by a third-party inspection agency for the equipment to be manufactured in Taiwan. Despite facing communication challenges, we successfully passed the Factory Acceptance Test (FAT) due to our effective utilization of widely adopted web conferencing tools.
Equipment before being delivered from the manufacturer's yard
In mid-June to early July 2023, as the global pandemic started to subside, commissioning took place, and we went on-site as the commissioning supervisor. Despite facing challenging conditions of a hot and humid climate, various issues arose during the commissioning process. However, through effective communication and cooperation with licensors and vendors, we successfully addressed and resolved the encountered challenges, ultimately completing the commissioning successfully.
Verifying the concentration of exhaust gases after solvent recovery during the commissioning process