VOC Recovery Facilities
Based on multiple technologies we have cultivated through construction of VOC recovery facilities, we are able to propose a system meeting the gas volume and VOC concentration.
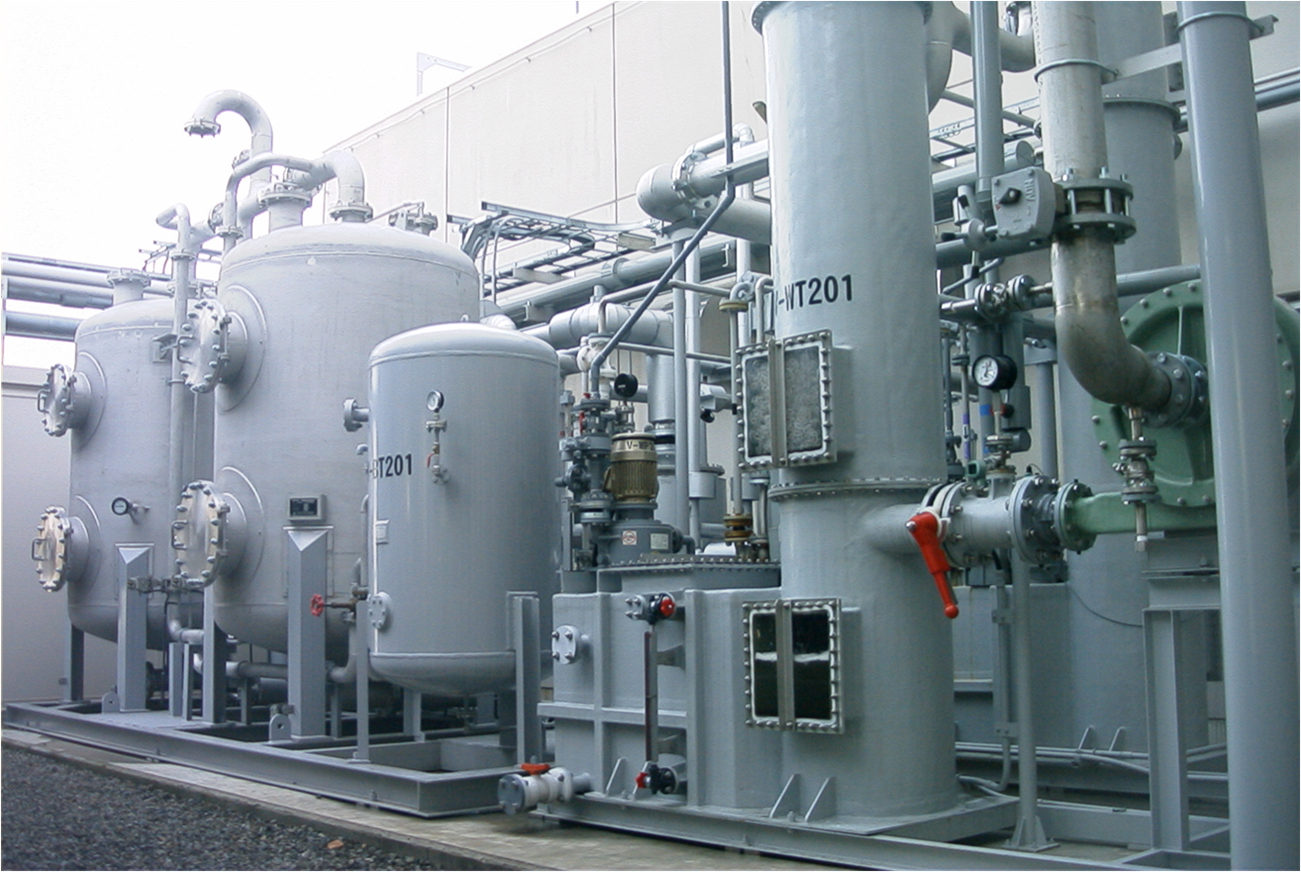
In order to recover expensive solvent for reuse under compliance with the PRTR Act and the Air Pollution Control Act, our system condenses and recovers exhaust gases containing volatile organic compounds (VOC) that are released into the air.
Features |
Compared to other methods such as the cryogenic method or the condensation method, our system can achieve high removal and recovery rates at a low running cost. With our various skills and technologies, we are able to propose the best system according to your specific requirements. |
---|---|
Benefits |
Recovery and reuse of VOC as liquid results in cost savings. |
Major Application |
VOC recovery |
Specifications | Applicable scope: Exhaust gas volume: - 1,000,000 m3/hr; VOC concentration: - 500,000 ppmv |
Processes and Methods | CAD-VRU1, CAD-VRU2, and CAD-VRU LL |
Combustion treatment usually requires fuels for combustion; however, our system can produce a cost advantage immediately after introduction by reusing recovered liquid.
We propose a different system based on concentration and air volume.
【CAD-VRU1】
Recovers gasoline by using adsorbent such as silica gel and zeolite
Features |
・Extremely safe ・Simple system ・Explosion-proof available ・Compact design ・Long lifetime of adsorption pH ・No catalytic action ・Easy operation and maintenance ・Ketone removable and recoverable |
---|---|
Benefits |
Highly efficient gasoline recovery |
Major Applications | Oil terminals and storage facilities |
Specifications | Gasoline recovery |
Processes and Methods |
Adsorption method |
【CAD-VRU2】
Removes and recovers VOC by using adsorbent such as silica gel and zeolite
Features |
・Extremely safe ・Simple system ・Explosion-proof available ・Compact design ・Long lifetime adsorption pH ・No catalytic action ・Easy operation and maintenance ・Ketone removable and recoverable |
---|---|
Benefits | Highly efficient VOC removal and recovery |
Major Applications |
Chemistry, painting, printing, electronics, and medical product plants Painting lines on automobiles and heavy electric machinery Oil terminals and storage facilities |
Specifications | VOC removal and recovery |
Processes and Methods |
Adsorption method |
【CAD-VRU LL】
Licensed by CMI Environment America、Inc. of the United States.
Adsorbs and separates VOC from VOC-containing exhaust gas, and recovers VOC as a solvent.
・Appropriate for the treatment of VOC-containing exhaust gases of middle to low concentration with a small to large amount of air volume.
・Recovery solvent can be reused.
・The amount of steam can be reduced by 40% by introducing this unique energy-saving system.
Features |
・Extremely safe ・Simple system ・Compact design ・Low operating cost ・Low pressure loss, and long lifetime activated carbon particles (Replacement period: About five years) ・Easy operation and maintenance ・Responds to various VOC-containing exhaust gases based on rich achievements |
---|---|
Specifications |
・Adsorbent is partial active carbon with the mesoporous structure ・Steam regeneration Temperature Swing Adsorption (TSA) ・The solvent recovery section is composed of a decanter separation, air stripping, or distillation separation according to the solvent property ・Solvent recovery rate: More than 95% ・Standard inlet VOC concentration: - 10,000 ppm |
Variations |
・Nitrogen regeneration TSA ・Energy-saving system achieved by the steam ejector/decompression distillation (Amount of Steam reduced by 40%) ・Large-scale system (independent reservoir type) 4,500 - 1,500,000 Nm3/h at maximum (40,000 - 50,000 Nm3/h per one adsorber) ・Middle-scale unit (integrated reservoir type) 3,000 - 60,000 Nm3/h ・Small-scale unit (skid-mount type) 150 - 4,500 Nm3/h ・Applicable to removal and recovery of BTX contained in drainage water |
Major Applications |
Removal and recovery of VOC discharged from facilities or plants for painting, printing and inks, adhesive agents, industrial cleaning agents, chemical products, rubber products, and clothing cleaning
Benzene, toluene, xylene, trimethylbenzene, ethyl acetate, decane, dichloromethane, MEK, trichloroethylene, IPA, butyl acetate, acetone, MIBK, n-hexane, n-butanol, n-pentane, cyclohexane, tetrachloroethylene, propyl acetate, nonane, chloromethane, styrene, etc. |
CMI Environment America、Inc.
(2525 Cabot Drive Suite205 Lisle, Il USA)
CMI Environment America、Inc. is a U.S. engineering firm with a small number of selected elite engineers, which was derived from a major French active carbon manufacturer, CECA (currently in the ARKEMA Group). AMCEC INC. has specialized in adsorption and recovery systems for VOC (solvents) contained in the gas phase and liquid phase by using active carbon and zeolite. This firm has valuable know-how, having delivered their systems to more than 1000 facilities for about 80 years including the times of its predecessor, CECA.