Taiyo Oil Co., Ltd.: Internal Inspection Work of 28B Submarine Pipeline
Project data
- Customer Name
- Shikoku Operations of Taiyo Oil Co., Ltd.
- Company Address
- Imabari City, Ehime Pref.
- Construction Name
- Internal Inspection Work of 28B Submarine Pipeline at Sea Berth
- Date of Completion
- Sep. 2014
- Pipe Quantity
- 28B x App. 500m
Maintenance of Submarine Pipeline with Sacrificial Anodes
We removed the sacrificial anodes after cleaning and then inspected, and repaired the inside of the submarine pipeline for the sea berth constructed in 1980. We have extensive experience in cleaning, inspecting, and repairing submarine pipelines. However, because the sacrificial anodes were installed in the pipeline at five-meter intervals in this case, the anodes hindered the performance of ordinary pig cleaning. The key factors in this case were how to clean the pipeline to enable the hot work and how to complete anode removal throughout the pipeline on schedule without incident. Because of the difficulty in resolving these issues, we met with the customer and subcontractor to discuss the plans for the work in detail over the course of a year and used mock-up piping for confirmation test prior to the actual work. The project was completed safely on schedule. Since the obstacle to the pig cleaning was eliminated, the pipeline can be maintained in the same condition as ordinary submarine pipelines in the future.
Advanced Confirmation Test with Mock-up Pipe
A pig launcher, receiver, and full-sized mock-up piping (28B) with dummy sacrificial anodes installed were fabricated one year before the actual work. The internal cleaning, cutoff, and removal of the anodes were performed experimentally. As a result, valuable data were acquired on the method for internal cleaning, time required to cut off the anodes, methods for removal and transfer of the anodes, and the required tools. Cleaning staffs could anticipate that the project could be completed safely and on time through the test.The pig launcher and pig receiver used in the test were used for the actual work.
Temporary Work: Removal of Submarine PLEM (Pipe Line End Manifold)
After the last unloading of the crude oil, the pipeline was washed out and the residual crude oil in the pipeline was thoroughly replaced to seawater. The project started with the large-scale temporary work of disassembly and landing of the PLEM buried at a depth of approximately seven meters under the seabed and installation of the underwater pig receiver. The thick protective coating (vinyl ester resin containing glass flakes) on the inner walls of the PLEM header at the time of construction remained intact. This proves the high durability of the coating.
After typhoon No. 8 passed, a floating crane (150 t), barge (2,000 kl), diving boat, and patrol boat were maneuvered into place, temporary facilities for the ground and undersea work were constructed, and pipeline cleaning started on a 24-hour basis.
Worksite - Near side: Pipe bridge on ground, Far side: Submerged PLEM (Indicated with circle)
Temporary facilities for pipeline cleaning (Left: Pig launcher on ground, Right: Floating crane at sea)
[Cutoff, Removal, and Carryout of Anodes with Inspection and Repair of Pipeline] Completed!
The barge (2,000 kl) was stand-by at sea and the pipeline was cleaned using a combination of chemical foam cleaning and pig cleaning. Next, the elbow at the upper side of splash zone was cut, and temporary equipment was set up to enter the pipeline. The pipeline was continuously ventilated with dry air, the concentrations of O2, HC, and H2S were monitored and work in the pipeline started on a 24-hour basis. The workers were divided into three groups. Group A was in charge of cutting off the anodes and the inspection. Group B was in charge of removing the anodes. Group C was in charge of the repair and application of the protective coating. The work was completed without incident before typhoon No. 11 hit the area. Since the anodes were removed, ordinary pig cleaning, inspections with an intelligent pig and repairs can be performed in the future.
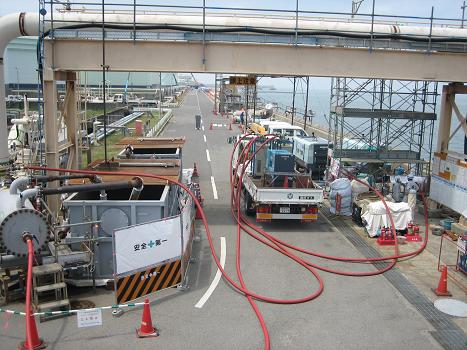
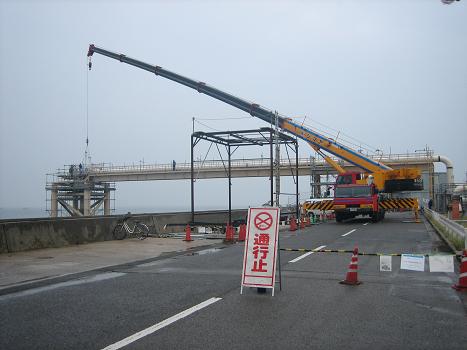